Heavy Duty Slurry Pumps
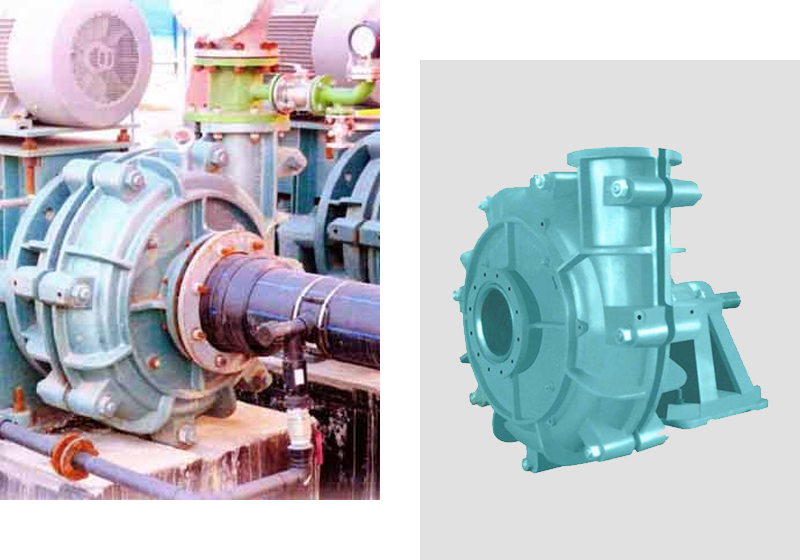
Capabilities & Design Features
Heavy Duty Slurry Pumps are designed for long life, efficient operation, and ease of maintenance resulting in a lower total cost of operation.
Pumps are available in either OXY-PRO Poly or Metal lined utilizing Abrasive and Corrosive Resistant Materials
An Optional heavy duty bearing assembly is available from UMA for applications where additional power required.
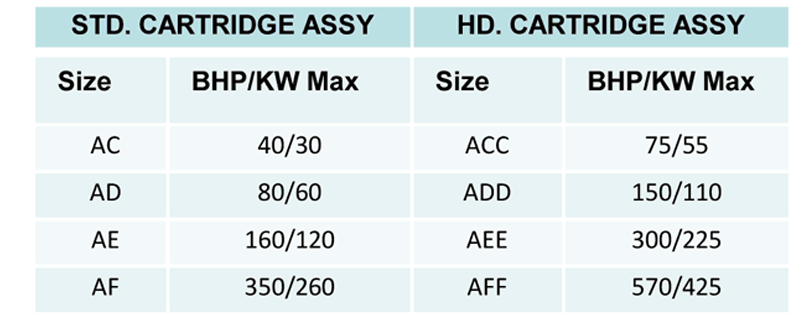
Cartridge Bearing Assembly and Shaft
The shaft is designed with a short overhang to:
Reduce shaft deflection.
Minimize vibration
Provided with hardened shaft sleeve to protect the shaft.
Optional dimensionally interchangeable heavy duty
bearing cartridge assemblies
Cartridge assembly is retained on a one piece frame
Grease purged piston rings to help seal contaminates
out of bearing housing.
Impeller
Enclosed impellers to maximize efficiency
Pump out vanes on both shrouds
Minimizes recirculation
Reduces stuffing box pressure
OXY-PRO or Hard Metal wet ends
Interchangeable hard metal and
OXY-PRO Impellers
Cast-in impeller threads to protect shaft
Impeller clearance set by moving cartridge assembly.
Double casing with radial split outer casing
Ease of assembly and disassembly of wet end.
Optional ductile iron construction for higher working pressures.
Removable liners are positively attached with fasteners.
Dynamic Seals
Reduces or eliminates need for seal water.
Reduces sleeve wear and possible bearing failure.
Removable Liners
Liners are positively attached utilizing studs
UMA OXY-PRO®
Exceptional wear life and chemical resistance for your pumps
Reduce Costs
Cost life effective & Reduced stock holding due to extended service life
Chemical Resistance
Highly resistant to swelling from chemical attack.
Eliminate Downtime
Extended life OXY-PRO of wet end parts eliminates pump stoppages.
Increase life
OXY-PRO has increased pump wet end life up to ten times (depending on application)
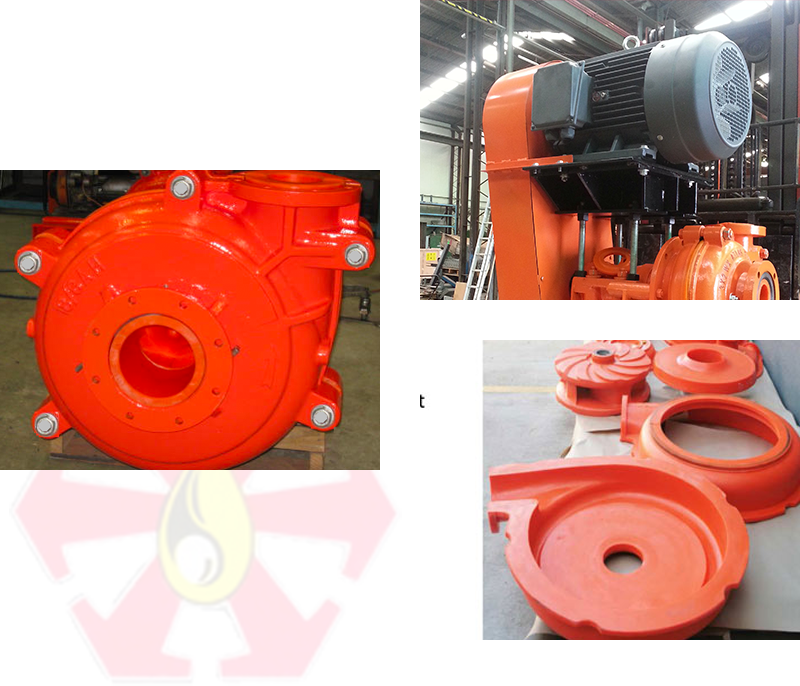
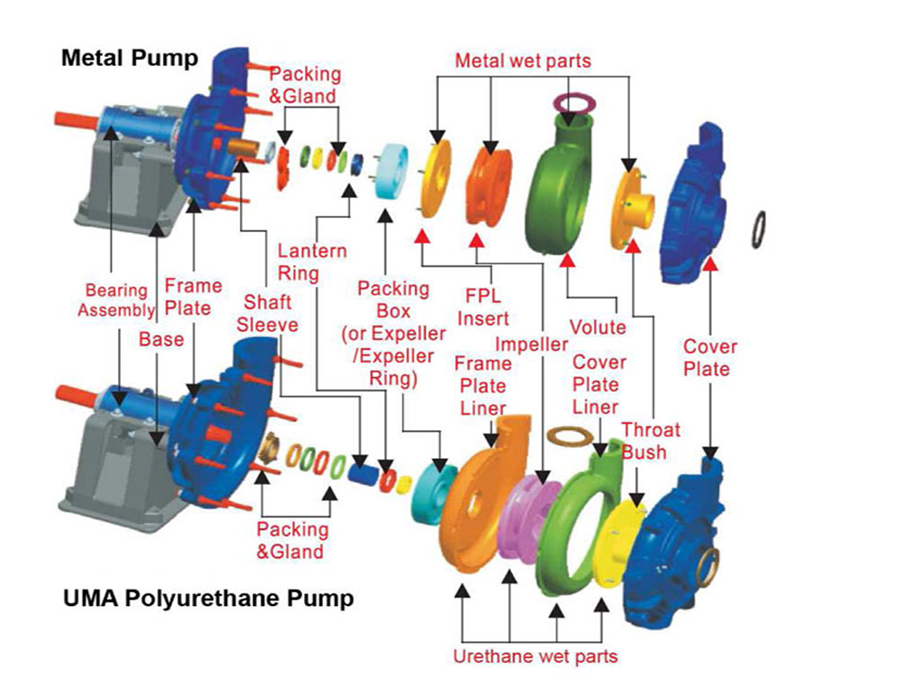
Pump configuration
The pump liner and impeller material have
interchangeable wear part combinations.
Liners and impellers for hard metal and OXY-PRO lined
pumps have common dimensions and are
interchangeable within the same pump size.
Frame supports the bearing cartridge which includes
grease lubricated taper roller or cylindrical bearings.
Bearings are located on a large diameter shaft designed
to minimize overhang and deflection.
For conventional packed box and lantern ring
construction, sealing water must be provided at a
minimum of 10 PSIG above discharge pressure to insure
positive flow.
Where suction conditions allow. UMA’s expeller seal
can eliminate the need to supply water to the stuffing
box. Where high suction pressures or series pumping is
desired other methods of sealing must be utilized.
Expeller and expeller ring are constructed from Hi Chrome material.
Shaft sleeve material is 420 SS hardened to 550 Brinell
to protect the shaft from wear.
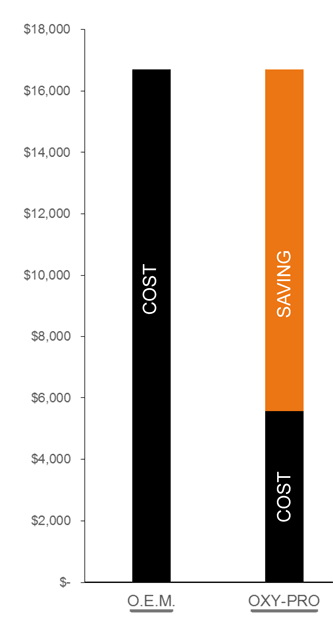
Cost Savings
The recorded running hours between replacement of chrome steel and rubber wet end parts averaged 750 hours, at a cost of $3,709 per set.
UMA OXY-PRO®
wet end parts lasted 7,500 hours (10 times longer) at a cost $5,565 per set.
The cost of rubber or steel parts to run
7,500 hours was $37,090. The mine Has saved $31,525 on just one pump in 10 months.
Components Structure & Graphs
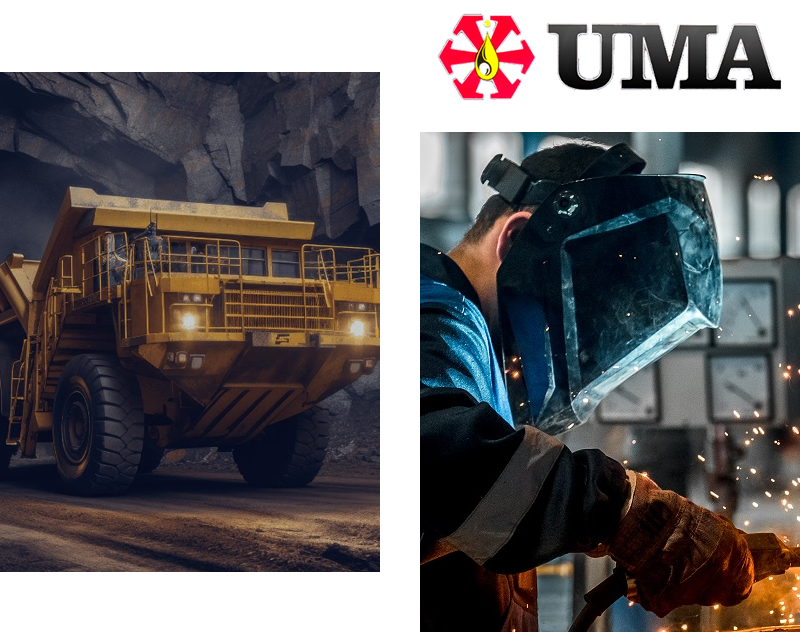
Contact Us
Urethane Manufacturers of Australia Pty Ltd (UMA) has proudly emerged as the unrivaled leader in Australasia’s mineral processing industry. With a rich history spanning four decades, UMA has become synonymous with quality, reliability, and innovation in the supply of Replacement Parts for Mineral Process Equipment, Accessories, and Coatings.